一种基于双神经网络逆模型的屛式过热器汽温控制方法与流程



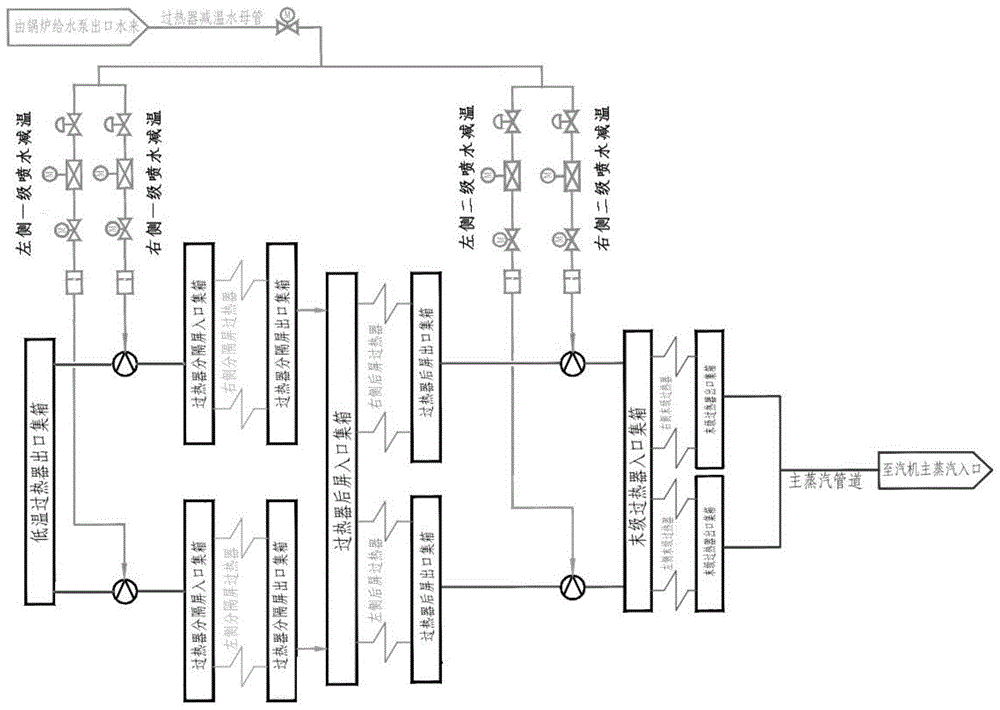
本发明属于电站锅炉过热汽温控制技术领域,尤其涉及一种基于双神经网络逆模型的屛式过热器汽温控制方法。
背景技术:
过热蒸汽温度是燃煤锅炉运行中的关键参数,必须控制在规定范围内,过热汽温过高或过低会直接影响锅炉机组的安全经济性。大容量锅炉过热器系统一般均配置了至少两级的混合式喷水减温器。控制系统通过计算各级过热器出口汽温实际值和设定值的偏差,经过pid控制算法输出指令来控制喷水阀开度,改变减温水量来调节各级过热器出口汽温。
由于大容量锅炉机组经常处于深度调峰大幅变工况运行,且过热汽温系统是一个典型的非线性、大惯性、大时延的被控对象,常规的单回路pid过热汽温控制策略很达到预期的控制效果。因此现有的过热器喷水减温系统,各级过热汽温多采用串级pid控制方案。该方案根据过热器出口温度设定值t2sp和实际汽温t2的偏差,由外环主pid调节器实时计算出喷水减温器后温度的设定值(副调)t1sp,再根据此副调设定值t1sp与喷水减温器后实际温度t1的偏差,由内环副调pid来调节喷水减温阀开度μ,控制喷水后的汽温t1与内环设定值t1sp一致。通过外环主回路pid和内环副回路pid协同作用,达到精确控制过热器出口汽温t2的目的。
在针对屛式过热器(过热器1级减温系统)采用上述串级控制方案时,正常情况下1级喷水减温器后的汽温t1(屛式过热器入口)均应有一定的过热度,减温器的出口汽温t1会随喷水量的增加不断下降。但实际运行中,一些亚临界锅炉存在严重的偏烧现象,会导致两侧屛式过热器受热非常不均匀。受热多的一侧屛式过热器,为了控制屛式过热器出口汽温不超限,某些情况下喷水量很大,导致1级减温器后的温度t1接近或到达饱和蒸汽区,才能保证屛式过热器出口汽温t2不超限。根据蒸汽的热力学特性,当喷水后的蒸汽接近饱和蒸汽区时,t1不会再随着喷水量的增加而降低,而是维持当前汽压对应的饱和温度tbh基本不变。此时导前温度t1对喷水量不再敏感,使得内环的pid动作失去依据。由于导前汽温t1无法跟踪内环设定值t1sp,且屛式过热器本身具有大惯性、大时延特性,若喷水量继续加大,很容易导致屛式过热器出口汽温t2大幅降低,威胁机组的安全运行。
技术实现要素:
本发明的目的是提供一种基于双神经网络逆模型的屛式过热器汽温控制方法,以克服现有屛式过热器蒸汽温度控制方法对机组大范围变工况适应性差,特别是当锅炉存在严重偏烧,导致喷水后汽温接近饱和蒸汽区时导前温度失灵的问题,增强工况适应性,有效应对喷水后蒸汽接近饱和区时温度对喷水量不敏感,引起屛过出口汽温控制效果变差的问题。
本发明提供了一种基于双神经网络逆模型的屛式过热器汽温控制方法,包括如下步骤:
步骤1,基于屛式过热器汽温对象特性,建立基于神经网络的第一逆模型及第二逆模型;
步骤2,基于第一逆模型建立外环为神经网络逆控制,内环为pid控制的第一控制策略;基于第二逆模型建立神经网络逆前馈控制器,并用pid控制器进行补偿控制的第二控制策略;
步骤3,在机组实际运行中,根据喷水减温后的屛过入口汽温所处状态在第一控制策略与第二控制策略之间进行自动选择:若处于过热区,选择第一控制策略进行汽温实时控制;若接近饱和区则自动切换为第二控制策略进行汽温实时控制。
进一步地,所述步骤1包括:
1)确定所述第一逆模型及第二逆模型的输入和输出参数;
所述第一逆模型的输入参数包括负荷ne、燃料量bf、总风量fa、燃烧器摆角β、屏过出口汽温实际值t2,输出参数为一级喷水减温器出口汽温t1;所述第二逆模型的输入参数包括负荷ne、燃料量bf、总风量fa、燃烧器摆角β、高加出口给水压力pw、高加出口给水温度tw、过热蒸汽压力ps或汽包压力pq、低过出口汽温t0、屏过出口汽温实际值t2,输出参数为一级喷水阀开度u;
2)从现场dcs系统获取机组的历史运行数据,从中选取用于所述第一逆模型及第二逆模型建立和验证的样本数据;所述样本数据包括机组协调系统自动升降负荷的最低负荷至额定负荷期间的典型稳态工况,以及多个升降负荷周期的动态过渡工况,且保证建模所需各变量均充分地激励;
3)确定建模采用的神经网络类型及模型结构,建立所述第一逆模型及第二逆模型,并运用获取的机组历史运行数据完成逆模型的训练和检验。
进一步地,所述步骤2)包括:
从dcs历史运对模型训练样本输入、输出进行归一化处理,并采用归一化后的样本训练模型,再将模型输出反归一得到实际工程单位的变量值,具体的归一化公式为:
y=(ymax-ymin)*(x-xmin)/(xmax-xmin)+ymin;
式中:x,y分别为参数的实际值和标称值,xmin、xmax分别为训练样本集数据中参数x的最小值和最大值,ymin、ymax分别为归一化处理后参数的最小值和最大值。
进一步地,步骤3)中所述模型结构的确定方法包括:
对于第一逆模型和第二逆模型,分别建立具有j个输入参数(u1,u2,…,uj)和一个输出参数y的非线性自回归滑动平均预测模型,且设定模型在k时刻的输出参数y(k)与模型各输入参数ui在k时刻和过去n个时刻的值ui(k)、ui(k-1),…,ui(k-n)及输出参数y在过去m个时刻的值y(k-1),y(k-2),…,y(k-m)相关,其结构的具体表达式为:
y(k)=g[y(k-1),...,y(k-m);u1(k),u1(k-1)...,u1(k-n);...;uj(k),uj(k-1)...,uj(k-n)]。
进一步地,步骤3)中所述逆模型的训练和检验包括:
分别针对不同输入、输出时延阶次n、m取值,通过比较具有不同隐层单元数神经网络模型的收敛性能,确定隐层神经元个数,具体包括:依次增加隐层神经元个数,对具有不同隐层单元数的模型,设置同样的训练周期、训练方法、训练参数及最小均方误差指标,分别对各模型进行训练,比较训练完成后各模型输出在整个训练样本集的mse,在满足mse精度指标的前提下,选择隐层单元较少的模型为优化的模型结构,最终建立满足mse指标的n*m个模型;
在不同n、m取值的共n*m个模型均训练完成后,选取与训练样本不同的历史数据,对训练好的模型进行测试,对不同模型的输出预测值和样本实际值进行比较,采用预测数据的最大误差绝对值、平均绝对误差、均方误差评估模型的预测性能,确定模型的最优时延阶次n、m取值,从而找到最优的模型结构。
进一步地,所述步骤3包括:
①实时监测屛式过热器减温喷水压力pw及一级减温器后的屛式过热器进口温度t1,根据pw动态计算对应的蒸汽饱和温度tbh,并比较tbh和t1的大小,判断喷水后汽温t1是否接近饱和区;
②若一级减温器后的温度t1≥tbh+δ,δ为裕度值,表明喷水后汽温t1处于过热区且具有一定的裕度,则选择所述第一控制策略,具体包括:利用第一逆模型,根据机组负荷ne、燃料量bf、总风量fa、燃烧器摆角β、屏过出口汽温实际值t2及屏过出口汽温设定值t2sp,计算屛过入口喷水减温后汽温期望值t1exp作为内环副调pid的设定值t1sp;根据屛式过热器进口温度t1和t1sp的偏差,利用内环pid控制器,改变喷水减温阀开度指令u,调节喷水后起汽温t1,此时第二控制策略不起作用,且输出处于跟踪状态;
③若一级减温器后的温度t1<tbh+δ,表明喷水后汽温接近饱和区对喷水量不再敏感,则自动选择所述第二控制策略,具体包括:利用第二逆模型,根据机组负荷ne、燃料量bf、总风量fa、燃烧器摆角β、高加出口给水压力(1级减温器喷水压力)pw、高加出口给水温度tw、过热蒸汽压力ps或汽包压力pq、低过出口汽温t0、屏过出口汽温实际值t2及屏过出口汽温设定值t2sp,计算喷水减温阀开度前馈指令uf,送入反馈补偿pid的前馈输入端口;根据屛式过热器出口温度t2和t2sp的偏差,利用内环pid控制器,计算喷水减温阀开度补偿指令ub;将前馈逆控制器指令uf和反馈补偿控制器指令ub叠加,得到一级喷水减温阀开度总指令u,直接改变喷水减温阀开度,实现屛式过热器出口汽温t2控制,此时所述第一控制策略不起作用,且副调pid输出处于跟踪状态。
进一步地,在将屏过出口汽温设定值t2sp作为参考值输入之前增加参考值t2ref动态计算环节,其计算公式如下:
t2ref(k)=f(t2(k),t2sp(k),ksat);
式中:t2(k)为k时刻屛式过热器出口汽温实际值;t2sp(k)为k时刻dcs系统屛式过热器出口汽温设定值;t2ref(k)表示k时刻逆控制器的参考值;ksat为参考值校正强度系数。
借由上述方案,通过基于双神经网络逆模型的屛式过热器汽温控制方法,能够应对导前温度失灵问题,提高屛式过热器汽温控制对亚临界燃煤锅炉存在严重偏烧情况及机组大幅变工况运行的适应能力。
上述说明仅是本发明技术方案的概述,为了能够更清楚了解本发明的技术手段,并可依照说明书的内容予以实施,以下以本发明的较佳实施例并配合附图详细说明如后。
附图说明
图1是本发明所涉及的过热器喷水减温系统流程图;
图2是本发明具有外部时延的神经网络逆模型通用结构图;
图3本发明两种不同智能控制策略及自动切换原理图。
具体实施方式
下面结合附图和实施例,对本发明的具体实施方式作进一步详细描述。以下实施例用于说明本发明,但不用来限制本发明的范围。
本实施例提供了一种基于双神经网络逆模型的屛式过热器汽温控制方法,包括如下步骤:
步骤1,基于屛式过热器汽温对象特性,建立基于神经网络的第一逆模型及第二逆模型;
步骤2,基于第一逆模型建立外环为神经网络逆控制,内环为pid控制的第一控制策略;基于第二逆模型建立神经网络逆前馈控制器,并用pid控制器进行补偿控制的第二控制策略;
步骤3,在机组实际运行中,根据喷水减温后的屛过入口汽温所处状态在第一控制策略与第二控制策略之间进行自动选择:若处于过热区,选择第一控制策略进行汽温实时控制;若接近饱和区则自动切换为第二控制策略进行汽温实时控制。两种控制策略根据条件判断自动选择,并实现相互跟踪,无扰切换。
本发明充分考虑了运行中各种干扰因素对屛式过热器汽温的影响,并可有效避免锅炉严重偏烧时喷水量过大,喷水后汽温接近饱和区致使导前温度不敏感影响汽温控制效果的问题,可有效改善屛式过热器汽温控制效果,提高锅炉运行的安全性及快速变负荷适应能力。
现以某亚临界锅炉屛式过热器一级喷水减温系统建模和控制策略实现为例,详细说明上述方法的实施步骤。
a.建立两种2种不同结构屛式过热器汽温对象逆模型。
具体步骤如下:
(1)确定过热器一级喷水减温系统2种逆模型建立所需的输入、输出变量,并核实2种模型建立所需现场原始信号的准确性及工程单位,涉及到的主要变量如下表所示(根据锅炉型号结构不同,不限于此)。
2)从现场dcs系统获取机组的历史运行数据,从中选取用于屛式过热器喷水减温系统2个逆模型建立和验证的样本数据。
3)确定建模采用的神经网络类型及模型结构,建立屛式过热器汽温对象的2个逆动态模型,并运用获取的机组历史运行数据完成逆模型的训练和检验。
2个逆模型建模的具体步骤如下:
①确定2个逆模型的输入和输出参数
逆模型1用于反映一级过热器喷水减温器后的蒸汽温度t1与屛式过热器出口温度t2的逆动态特性,适用于喷水后蒸汽温度t1处于过热区,屛式过热器进、出口温度存在较好逆对应关系的运行工况。该第一逆模型应用于主回路采用神经网络逆控制器、副回路为采用pid控制器的串级智能控制方案(第一控制策略),因此逆模型建立仅针对过热器本身的温升特性,不包含喷水环节在内。
逆模型1的输入、输出变量见下表。
逆模型2用于反映屛式过热器一级喷水减温阀开度μ(%)与过屛式热器出口温度t2的逆动态特性,适用于随喷水量增加,喷水后蒸汽已接近饱和蒸汽区,喷水后汽温t1对喷水量不再敏感的运行工况。此模型适用于包含喷水环节在内的过热器整级前馈逆控制加pid补偿的智能控制策略方案(第二控制策略)。
逆模型2的主要输入、输出变量如下表。
②确定2种逆模型的结构
在建立逆模型1(逆模型2)时,并非直接利用上述5个(9个)输入参数、1个输出参数来建模,而是以前向多阶层神经网络(如bp神经网络)为基础,采用具有j个输入参数(u1,u2,…,uj)和1个输出参数y的非线性自回归滑动平均(narma)模型结构,且认为模型在k时刻的输出参数y(k)与模型各输入参数ui在k时刻和过去n个时刻的值ui(k)、ui(k-1),…,ui(k-n)及输出参数y在过去m个时刻的值y(k-1),y(k-2),…,y(k-m)相关,该非线性模型的具体表达式如下:
y(k)=g[y(k-1),...,y(k-m);u1(k),u1(k-1)...,u1(k-n);...;uj(k),uj(k-1)...,uj(k-n)];
上述模型采用神经网络具体实现时,建立的模型具有与被建模非线性系统相同的结构,即:
这里,n、m具体取值根据对象的特性,经模型优化实验后确定。
③模型训练及校验样本的获取和数据预处理
在模型训练样本选取方面,为使逆模型1(逆模型2)全面反映屛式过热器的温升逆特性(喷水减温逆特性),选取的样本数据应包含模型将来实际应用时的机组负荷调节范围,并能正确反映各种输入扰动下的负荷变化特征。
为保证2个逆模型较完整地反映过热汽温系统的变工况特性,样本数据包含的负荷工况应尽量宽,应包含机组协调系统自动升降负荷的最低负荷至额定负荷期间的典型稳态工况以及多个升降负荷周期的动态过渡工况,且保证建模所需各变量均应充分地激励,确保获取的训练样本数据工况较为全面、各输入参数的激励较为充分。根据此原则,从dcs历史运行数据中提取并选择用于2个逆模型训练和检验的训练样本集和校验样本集。
考虑各输入参数的正常变化幅度差别较大,为防止“大数吃小数”均衡反应各输入参数变化对模型输出的影响,建模前需要对模型训练样本的输入、输出数据进行归一化处理,并采用归一化后的样本训练模型,并将模型输出反归一以得到实际工程单位的变量值。具体的归一化公式为:
y=(ymax-ymin)*(x-xmin)/(xmax-xmin)+ymin;
式中:x,y分别为参数的实际值和标称值,xmin、xmax分别为训练样本集数据中参数x的最小值和最大值,ymin、ymax分别为归一化处理后参数的最小值和最大值。
④用训练样本集对模型进行训练,并采用与训练样本不同的验证样本集完成模型的检验。根据实验结果,反复优化模型的结构和参数,保证模型具有较高的预测精度和良好的泛化能力。应注意,模型检验时验证样本集的各输入、输出参数应采用训练集数据各变量的最小值和最大值进行归一和反归一处理。
逆模型1和逆模型2训练的基本原理是基于误差反向传播(bp)算法。该算法分为正向传播和反向传播两个阶段。以逆模型1为例,正向传播阶段从样本集中取第i个样本[ne,bf,fa,β,t2,t1]i,将xi=[ne,bf,fa,β,t2]i输入网络,计算相应的实际输出oi。反向传播阶段计算实际输出oi与相应的样本输出t1i的差,并按极小化网络模型输出误差mse的方式调整神经网络权值矩阵。设模型样本集共包含s组输出样本对,则负荷预测模型在整个样本集上的均方误差mse定义如下:
采用bp算法训练模型的信息正向传播与误差反向传播的各层权值调整的过程是针对样本集周而复始进行的,直到网络输出的误差mse减小到可以接受的程度,或达到预先设定的学习次数为止。为提高网络收敛速度,防止训练陷入局部最小,以bp算法为基础,出现了多种改进算法,其中l-m(levenberg-marquardt)优化算法(trainlm)与其他误差梯度算法相比,具有最快的收敛速度,因此,这里选用l-m算法为模型的训练算法。
借助matlab和神经网络工具箱利用newff函数创建机组负荷的预测模型,网络选取具有1个输入层、1个隐含层和1个输出层的3层结构,隐层激励函数选用tansig,输出层激励函数选用purelin。当模型的输入输出变量和网络结构确定后,采用narma模型建立负荷预测神经网络模型的主要任务是优化输入、输出时延的阶次n、m以及合理确定神经网络的隐层接点、权值矩阵、阈值等参数。
这里,神经网络模型优化分为离线训练和离线校验两个阶段。第一阶段:采用训练样本集分别针对不同输入、输出时延阶次n、m取值,比较具有不同隐层单元数神经网络模型的收敛性能,确定合适的隐层神经元个数,建立满足mse指标的n*m个模型。第二阶段在不同n、m取值的共n*m个模型均训练完成后,利用与训练样本集不同的校验样本对模型进行进一步校验,对不同情况下模型的预测精度进行比较,确定模型的最优时延阶次n、m取值,找到最优的模型结构。具体步骤为:
(1)分别针对不同输入、输出时延阶次n、m取值,通过比较具有不同隐层单元数神经网络模型的收敛性能,确定隐层神经元个数。具体做法是:依次增加隐层神经元个数,对具有不同隐层单元数的模型,设置同样的训练周期、训练方法、训练参数及最小均方误差(mse)指标,分别对各模型进行训练,比较训练完成后各模型输出在整个训练样本集的mse。在满足mse精度指标的前提下,选择隐层单元较少的模型为优化的模型结构,最终建立满足mse指标的n*m个模型;
(2)在不同n、m取值的共n*m个模型均训练完成后,选取与训练样本不同的历史数据,对训练好的模型进行测试,对不同模型的输出预测值和样本实际值进行比较,采用预测数据的最大误差绝对值、平均绝对误差(mad)、均方误差(mse)3项指标评估模型的预测性能,以确定模型的最优时延阶次n、m取值,从而找到最优的模型结构。
b.基于神经网络逆模型1和逆模型2,建立包含第一控制策略和第二控制策略的双重智能控制算法,并在算法中设置策略选择工况判断条件,实现两种方案的自动选择和切换。
上述控制策略实现方法如下:
①第一控制策略
该方案为神经网络串级控制方案,外环采用基于神经网络逆模型1的逆控制器为主控制器,内环采用经典pid控制器为副控制器。
主控制器根据机组当前时刻和前几个时刻的机组负荷ne、燃料量bf、总风量fa、燃烧器摆角β、屏过出口汽温实际值t1、屏过出口汽温设定值t2sp等,利用训练好的神经网络逆模型1计算屛过入口(喷水减温器后)汽温期望值t1exp,再将该汽温期望值t1exp用作内环副调pid控制器的设定值t1sp,根据该设定值t1sp与屛过入口实际汽温t1的偏差,改变喷水减温阀开度指令u,控制减温水量,调节屛过入口汽温t1。通过外环和内环控制器协同作用,从而达到调节屛过出口汽温的目的。
运用大量历史运行数据训练完成的屛式过热器神经网络逆模型1具有较高的精度,但考虑训练模型的结构及参数选取的不完善以及现场工况和干扰的复杂性,直接把屏式过热器出口汽温设定值t2sp作为串级外环主调神经网络逆控制器的参考值输入,不一定能够达到好的的控制效果,为此在前面增加一个参考值t2ref动态计算环节,其计算一般公式如下:
t2ref(k)=f(t2(k),t2sp(k),ksat);
式中:t2(k)为k时刻屛式过热器出口汽温实际值;t2sp(k)为k时刻dcs系统屛式过热器出口汽温设定值;t2ref(k)表示k时刻神经网络逆控制器的参考值;ksat为参考值校正强度系数,其大小决定了参考值围变化的范围和快慢,具体数值需结合现场试验加以确定。
副控制器采用具有前馈的经典增量式pid控制算法,其实现公式如下:
δu(k)=kp[e(k)-e(k-1)]+kie(k)+kd[e(k)-2e(k-1)+e(k-2)]+uf(k)-uf(k-1);
式中:kp为比例系数,ti为积分时间常数,td为微分时间常数。uf为其它改善汽温控制效果的前馈指令,可根据情况考虑是否引入。
②第二控制策略
该方案为由基于整级逆模型2的前馈控制器,和作为误差反馈补偿的pid控制器共同构成。
其中,神经网络前馈逆控制器根据机组当前时刻和前几个时刻的机组负荷ne、燃料量bf、总风量fa、燃烧器摆角β、高加出口给水压力(1级减温器喷水压力)pw、高加出口给水温度(1级减温器喷水温度)tw、过热蒸汽压力ps(或汽包压力pq)、低过出口汽温t0、屏过出口汽温实际值t2、屏过出口汽温设定值t2sp等,利用训练好的逆模型2计算喷水减温阀开度前馈指令uf;然后将前馈指令uf送至pid控制器的前馈输入端,再根据屏过出口汽温实际值t2和屏过出口汽温设定值t2sp的偏差进行精确补偿控制计算得到反馈补偿ub,将前馈逆控制器指令uf和反馈补偿控制器指令ub叠加,得到一级喷水减温阀开度指令u,直接改变喷水减温阀开度μ,实现屛式过热器出口汽温t2控制。
与第一控制策略类似,为取得好的的控制效果,同样在神经网络前馈控制器前面增加一个参考值t2ref动态实时计算环节,其一般表达式与式(3)相同。该方案中误差反馈补偿控制器也采用具有前馈的经典增量式pid控制算法,表达式与式(4)相同,不同之处在于uf来自神经网络前馈控逆控制器的输出。
③两种方案自动切换条件
首先,根据喷水减温器压力(过热器喷水压力)pw实时计算出该压力下对应的蒸汽饱和温度tbh,并考虑一定的裕度值δ,可得切换温度tqh=tbh+δ。
将喷水减温器后的蒸汽温度t1与tqh进行比较,若t1>=tqh,说明喷水后汽温尚处于过热区且具有一定裕度,屛式过热器出口温度t2和进口温度(喷水后)t1具有较好的逆对应关系,自动选择控制方案1的汽温串级智能策略进行喷水阀控制,此时控制器2输出处于跟踪状态;
若t1<tqh,说明喷水后汽温t1已接近饱和蒸汽温度tbh,喷水后温度对喷水量变化不再敏感,自动切换至控制方案2进行汽温控制,而控制方案1则转入输出跟踪状态。通过两种方案输出相互跟踪,可实现两种方案的无扰切换。
本发明根据当前的喷水减温后汽温所处区域,自动选取合适的第一控制策略或第二控制策略,充分发挥两种策略各自的优势,达到提高屛过出口汽温控制效果的目的。两种控制策略所依赖的逆模型1和逆模型2充分考虑了运行中各种干扰因素对屛式过热器汽温的影响,使得控制器具有较强的抗干扰能力。当锅炉严重偏烧时喷水量过大,导致喷水后屛式过热器入口汽温接近饱和区,串级智能控制策略1导前汽温失灵时,可及时切换为前馈加反馈补偿的第二控制策略,确保喷水减温阀及时动作,防止屛过出口汽温大幅下降。本发明可有效改善屛式过热器汽温控制效果,提高锅炉运行的安全性及快速变负荷适应能力。
上述技术方案各环节与现有技术相比具有以下特点:
1)在神经网络逆模型1和逆模型2参数的选取上,全面考虑了影响过热汽温的相关因素。逆模型1反映过热器温升逆特性,不包含喷水环节在内,模型输入至少包含燃料量bf、送风量fa、燃烧器摆角β等参数。模型2反映过热器喷水阀开度与过热器出口温度关系的逆特性。由于减温器喷水压力pw、喷水温度tw、过热蒸汽压力ps(或汽包压力pq)等会影响减温水的流量和温度从而影响屛式过热器出口汽温t2,模型输入中应包含这些参数;为增强模型适应性,喷水减温阀前的过热汽温也作为输入参数包含在模型2输入中。在模型1和逆模型2的输入中均增加机组负荷ne这一参数,有助于更准确地反映机组当前的运行工况,提高模型在变负荷动态过程参数预测的及时性和准确性。
2)训练样本数据中包含机组自动升降负荷可达范围内,不同稳态工况和不同变负荷动态过渡工况的历史运行数据,且训练样本包含的数据中各模型输入变量均应充分激励,保证建立的模型可全面反映喷水减温系统的静、动态特性,反映各输入参数变化对输出的影响。
3)神经网络模型结构上,不是采用单纯的的静态网络(如bp、rbf网络)或递归型网络(如elman网络),而是以这些网络为基础,在神经网络输入中增加输入变量的n阶外部时延,以及输出变量的m阶反馈时延,形成非线性自回归滑动平均(narma)预测模型结构。该模型结构对动态过程具有良好的建模能力,较快的收敛速度。通过模型试验确定各变量的合理时延阶次,可确保模型具有较高的预测精度和泛化能力,以适应不同变负荷率的变工况过程,达到更好的控制应用效果。
4)用训练好的过热汽温系统逆模型1和逆模型2构建控制器时,用可变的温度参考值t2ref来代替模型训练时所用过热器出口实际汽温t2,而其它相关输入变量和扰动参数,包括燃料量bf、送风量fa、喷水压力pw、喷水温度tw、过热蒸汽压力ps(或汽包压力pq)等则取自dcs的实时数据,并在程序内部自动迭代记忆各变量的时延值供模型实时预测计算使用。
5)在基于神经网络逆模型1的串级智能控制策略1和基于神经网络逆模型2的智能前馈加反馈补偿控制策略2中,温度参考值t2ref的计算均引入误差实时反馈,根据屛过出口汽温实际值t2和设定值t2sp的偏差,采用非线性函数对模型的输入汽温参考值t2ref进行动态计算,且其校正强度可由ksat调节。合适的误差校正强度ksat可保证控制器具有较小的控制误差又不致振荡。采用非线性修正函数与线性函数相比,误差增大时,控制器控制动作更加迅速,而误差较小时动作更加平稳,有效改善控制器的控制品质。
验证本发明效果的仿真研究对象为已投运的国产600mw亚临界机组,其过热器喷水减温系统的简化流程如图1所示。
参图2所示,对应于逆模型1,建模时考虑模型5个输入变量(机组负荷ne、燃料量bf、总风量fa、燃烧器摆角β、屏过出口汽温实际值t2)在k时刻的值及过去k-1,…,k-n时刻的值,以及屛过入口喷水减温后汽温t1在过去k-1,…,k-m个时刻的值对k时刻汽温t1的影响,采用以bp神经网络为基础的narma模型建立了5*(n+1)+m个输入、1个输出的喷水减温后汽温t1预测模型。
参图2所示,对应于逆模型2,建模时考虑模型9个输入变量(机组负荷ne、燃料量bf、总风量fa、燃烧器摆角β、、高加出口给水压力(1级减温器喷水压力)pw、高加出口给水温度(1级减温器喷水温度)tw、过热蒸汽压力ps(或汽包压力pq)、低过出口汽温t0、屏过出口汽温实际值t2共9个输入参数)在k时刻的值及过去k-1,…,k-n时刻的值,以及一级喷水阀开度u在过去k-1,…,k-m个时刻的值对k时刻一级喷水阀开度u的影响,采用以bp神经网络为基础的narma模型建立了9*(n+1)+m个输入、1个输出的一级喷水阀开度u预测模型。
在本验证实例中,用于训练模型的样本数据提取自上述600mw亚临界机组dcs的历史运行数据。所提取的样本包括300mw至600mw期间稳态及升、降负荷的变工况数据。在matlab平台用newff函数分别构建逆模型1和逆模型2,并用trainlm算法完成模型训练,模型训练的目标误差设为1e-6。经比较不同n、m取值时模型的预测效果,最终选择n=2、m=2模型为最优模型结构,逆模型1包括17个输入、1个输出,20个隐层节点。逆模型2包括29个输入、1个输出、20个隐层节点。
参图3所示,该优化控制方法包含如下3个步骤:
(1)实时监测屛式过热器减温喷水压力pw及1级减温器后的屛式过热器进口温度t1,根据pw动态计算对应的蒸汽饱和温度tbh,并比较tbh和t1的大小,判断喷水后汽温t1是否接近饱和区。
(2)若1级减温器后的温度t1≥tbh+δ,说明喷水后汽温t1处于过热区且具有一定的裕度,此时选择基于逆模型1的串级智能控制策略1。首先利用逆模型1,根据机组负荷ne、燃料量bf、总风量fa、燃烧器摆角β、屏过出口汽温实际值t2及屏过出口汽温设定值t2sp,计算屛过入口喷水减温后汽温期望值t1exp作为内环副调pid的设定值t1sp;然后根据屛式过热器进口温度t1和t1sp的偏差,利用内环pid控制器,改变喷水减温阀开度指令u,调节喷水后起汽温t1。此时智能控制方案2不起作用,且输出处于跟踪状态。
(3)若1级减温器后的温度t1<tbh+δ,说明喷水后汽温接近饱和区,此时自动选择基于逆模型2的前馈+反馈智能控制策略2。首先利用逆模型2,根据机组负荷ne、燃料量bf、总风量fa、燃烧器摆角β、高加出口给水压力(1级减温器喷水压力)pw、高加出口给水温度(1级减温器喷水温度)tw、过热蒸汽压力ps(或汽包压力pq)、低过出口汽温t0、屏过出口汽温实际值t2及屏过出口汽温设定值t2sp,计算喷水减温阀开度前馈指令uf,送入反馈补偿pid的前馈输入端口;然后根据屛式过热器出口温度t2和t2sp的偏差,利用内环pid控制器,计算喷水减温阀开度补偿指令ub;最后,将前馈逆控制器指令uf和反馈补偿控制器指令ub叠加,得到一级喷水减温阀开度总指令u,直接改变喷水减温阀开度,实现屛式过热器出口汽温t2控制。此时智能控制方案1不起作用,且副调pid输出处于跟踪状态。
将投运前机组原屛过出口汽温控制效果与投运后屛过出口汽温控制效果进行对比后得出:采用本发明优化控制方法后屏过出口汽温动态偏差和稳态温差小,喷水阀动作更加平稳,屛过出口汽温的控制效果大幅改善。
以上所述仅是本发明的优选实施方式,并不用于限制本发明,应当指出,对于本技术领域的普通技术人员来说,在不脱离本发明技术原理的前提下,还可以做出若干改进和变型,这些改进和变型也应视为本发明的保护范围。
起点商标作为专业知识产权交易平台,可以帮助大家解决很多问题,如果大家想要了解更多知产交易信息请点击 【在线咨询】或添加微信 【19522093243】与客服一对一沟通,为大家解决相关问题。
此文章来源于网络,如有侵权,请联系删除


