一种高能推进剂用耐烧蚀且力学性能优异的绝热材料及其制备方法与流程



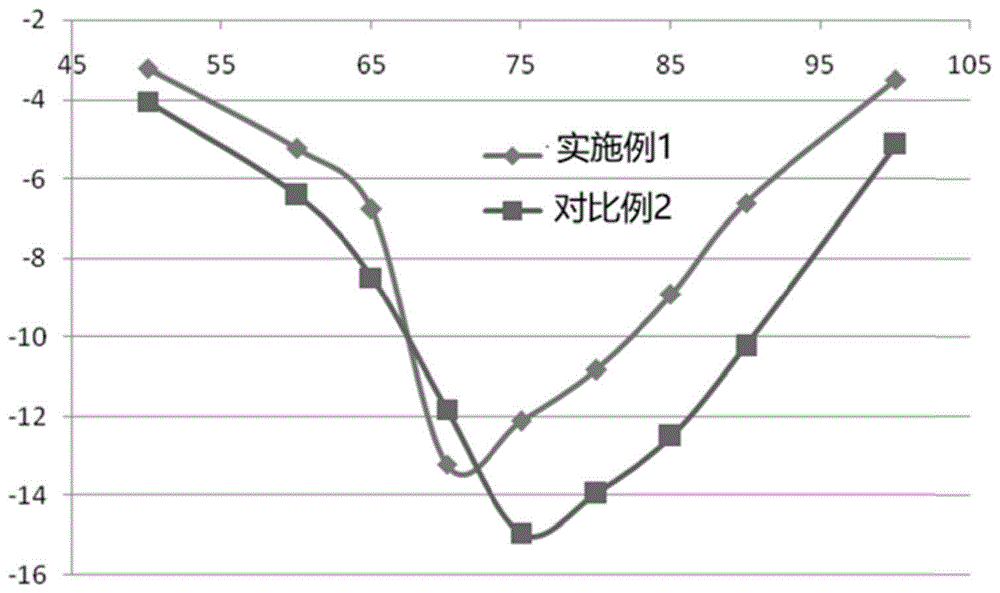
本发明属于耐烧蚀材料技术领域,特别涉及一种高能推进剂用耐烧蚀且力学性能优异的绝热材料及其制备方法。
背景技术:
固体火箭发动机内绝热层应当具有良好的力学性能,应能承受发动机在推进剂浇注与硫化、贮存、运输及飞行过程中所引起的各种应力的作用,如药柱在硫化后降温时因收缩产生变形产生的拉应力,发动机工作时的内压对绝热层的压应力,飞行过程中的短时大加速度和竖立储存中长时重力作用所引起的壳体-绝热层-药柱界面间的剪切应力等。
内绝热层应具有足够的伸长率以适应发动机增压及热循环应变的需要,发动机在点火的瞬间,内压由常压猛增至3~10mpa的工作压强,而为了提高发动机的质量比,燃烧室的壳体通常比较薄,刚性较差,所以,这种增压引起的应变是很可观的,复合材料壳体较钢壳体更为显著,如直径和长度均为800mm左右的中小型玻璃纤维/环氧壳体,在内压为4mpa时,前后接头间的轴向增量可达20~30mm,海神二级发动机在点火时,端盖处的轴向位移也超过20mm。假如绝热层没有足够的延伸率来适应这种冲击式的应变,则必将产生裂纹,导致发动机工作时发生穿火而使壳体受到热损伤。发动机在运输和储存过程中将遇到各种温度交变的环境而导致热应变的产生,由于内绝热层与壳体及推进剂的线膨胀系数差异较大,所以,必将出现壳体、绝热层与推进剂的线膨胀不协调的情况,这也要求内绝热层具有足够大的伸长率。
三元乙丙橡胶(epdm)在固体火箭发动机上应用时,为了满足耐烧蚀、抗冲刷等性能,达到保护壳体的作用,除了要求与壳体粘接性能较好以外,还要求epdm绝热层有较好的耐烧蚀性能和力学性能。epdm作为一种橡胶材料,其本身的耐烧蚀性能有限,无法满足固体发动机中高温、高压、高速气流对它的冲刷作用,为了达到使用要求,必须加入耐烧蚀填料、纤维材料、阻燃剂、补强剂及其它工艺助剂等以提高其耐烧蚀性能。纤维材料具有高强度、高模量、耐高温等优点;但是,未经处理的纤维表面呈现惰性,与橡胶的界面结合较差,增强效果有限,甚至能引起复合材料的自身缺陷。增加绝热层中纤维材料的用量能够提高耐烧蚀性能,但使用过多会使纤维填充橡胶材料存在明显的各向异性,影响绝热层力学性能的发挥,特别是使绝热层平行方向的断裂伸长率显著下降。
因此,为了提高绝热层的耐烧蚀性能,同时保证绝热层具有优良的力学性能以满足发动机实际生产过程的需要,研制一种耐烧蚀性能优良,并且具有较好的综合性能和成型工艺的绝热材料具有十分重要的意义。
技术实现要素:
为了克服现有技术中的不足,本发明人进行了锐意研究,提供了一种高能推进剂用耐烧蚀且力学性能优异的绝热材料及其制备方法,能够在纤维填充过多的情况下,仍然保持较好的力学性能,即各个方向上的力学性能基本一致,并不影响绝热层的其他性能,该绝热材料同时能够满足发动机对内绝热材料力学性能、粘接性能、耐烧蚀、以及抗冲刷性能等综合性能的要求,从而完成本发明。
本发明提供的技术方案如下:
第一方面,一种高能推进剂用耐烧蚀且力学性能优异的绝热材料,包括以下质量份的原料:
第二方面,一种高能推进剂用耐烧蚀且力学性能优异的绝热材料的制备方法,用于制备上述第一方面所述的高能推进剂用耐烧蚀且力学性能优异的绝热材料,包括以下步骤:
步骤1,向密炼机中按比例依次加入三元乙丙橡胶、补强剂、有机纤维、增粘树脂、阻燃剂、耐烧蚀填料、增塑剂、金属氧化物、硬脂酸、防老剂密炼至均匀混合;
步骤2,在双辊开炼机上,向步骤1的物料中按比例加入硫化剂和增粘剂进行混炼,然后薄通6-10次后,最后薄通均匀出片;
步骤3,将步骤2中获得产物,通过在平板硫化机130~160℃下硫化40~100min成型,优选160℃下硫化40min成型,每降低10℃硫化成型时间增加一倍。
根据本发明提供的一种高能推进剂用耐烧蚀且力学性能优异的绝热材料及其制备方法,具有以下有益效果:
(1)本发明中绝热材料及其制备方法,采用多种纤维并用技术途径,提高了epdm绝热材料在过载环境下抗高温粒子冲刷性能,满足发动机过载下对绝热层抗冲刷性能的要求;
(2)本发明中绝热材料及其制备方法,采用阻燃剂和耐烧蚀填料并用技术,提高了绝热材料的耐烧蚀性能及结碳强度,满足发动机过载下对绝热层耐烧蚀性能的要求;
(3)本发明中绝热材料及其制备方法,采用多种纤维及增粘剂体系,不仅满足发动机垂直方向的力学性能优异,且平行压延方向的伸长率依然较好,解决了纤维填充橡胶在不同方向力学性能差异过大的问题,保证了绝热层在不同条件下的性能可靠性,同时能适应发动机对绝热层力学性能的特殊要求;
(4)本发明中绝热材料,具有较低的密度(1.04-1.05g/cm3),使用该绝热材料作为发动机的绝材料时,无需大幅增加绝材料的厚度,甚至可以减薄绝热层厚度,因此可以减少发动机的“消极质量”,增加导弹的射程,提高导弹的作战能力;
(5)本发明中绝热材料及其制备方法,采用增粘剂,能够显著改善纤维、白炭黑等填料与基体间的作用力,显著提高材料内部的结构完整性,从而提高绝热层的力学性能,同时对改善混炼工艺具有较好的效果;
(6)本发明中的绝热材料具有优异的工艺性能,材料流动性好,可用于普通的金属壳体复合材料壳体的缠绕工艺,除可用于发动机中对力学性能要求苛刻的绝热层,在民用隔热橡胶材料也有较好的应用前景,应用面较广。
附图说明
图1为本发明实施例和对比例绝热材料的弯管烧蚀情况图;
图2为本发明实施例和对比例的烧蚀结果图,其中图2a为实施例1烧蚀结果图,图2b为对比例2烧蚀结果图。
具体实施方式
下面通过对本发明进行详细说明,本发明的特点和优点将随着这些说明而变得更为清楚、明确。
根据本发明的第一方面,提供了一种高能推进剂用耐烧蚀且力学性能优异的绝热材料,包括以下质量份的原料:
在本发明中,所述三元乙丙橡胶为一种乙烯含量为50%-60%、第三单体乙叉降冰片烯(enb)或双环戊二烯质量含量为5%-12%的乙烯、丙烯及第三单体共聚体。
在本发明一种优选的实施方式中,所述补强剂选自二氧化硅(sio2)、炭黑、或者二者的组合物,优选为二氧化硅,更优选为白炭黑。
在本发明一种优选的实施方式中,所述有机纤维为长纤状或浆泊状的聚对苯二甲酰对苯二胺纤维(pa)、芳砜纤维(psa)、聚酰亚胺纤维(pi)、聚苯硫醚纤维(pps)、聚对苯撑苯并双恶唑纤维(pbo)、聚丙烯腈纤维(pan)或酚醛纤维(pf)中的两种及两种以上的组合物,特别是5-10mm长纤状聚酰亚胺纤维(pi)和聚对苯二甲酰对苯二胺纤维(pa)两者的组合物,且两者的质量比为(5~10):(4~8)。
本发明人经过研究发现,加入单一纤维,绝热层的耐烧蚀性能存在一定的极限,且随着纤维用量的增加,绝热层的力学性能下降显著,当将两种纤维及以上并用时,耐烧蚀性能提升显著,能够产生协同效应,而只加入一种纤维则不具有这种效果。
在本发明一种优选的实施方式中,所述增粘树脂为固体或液体的酚醛树脂、硼酚醛树脂、钼酚醛树脂、萜烯树脂中的一种或几种。
本发明中,增粘树脂的加入是为了提高该绝热材料制备的绝热层的成型黏性,经过研究发现,基于100份的三元乙丙橡胶,增粘树脂的用量在5-15份,绝热层能获得较好的成型黏性,同时在与金属、复合材料、硫化橡胶进行硫化黏合时,能够获得较好的粘接性能;若增粘树脂的用量过低且低于上述范围的最小值,则绝热层自身在混炼时的成型黏性较差,导致在开炼机上混炼困难,同时与其他界面的粘接性能也无法达到要求。相反的,若增粘树脂的用量过高且高于上述范围的最大值,则绝热层的成型黏性过高,不利于绝热层的出片以及后续的工艺性能,造成操作困难。
在本发明一种优选的实施方式中,所述阻燃剂为聚磷酸铵(app)或者硫酸铵。
在本发明一种优选的实施方式中,所述耐烧蚀填料选自球状或颗粒状的聚对苯二甲酰对苯二胺(pa)、芳砜(psa)、聚酰亚胺(pi)或聚苯硫醚(pps)中的一种或多种,优选为聚酰亚胺(pi)或聚苯硫醚(pps)。
本发明中,耐烧蚀填料的加入是为了提高该绝热材料制备的绝热层的耐烧蚀性能。经过研究发现,基于100份的三元乙丙橡胶,耐烧蚀填料10-30份,特别是10-15份时,绝热层的耐烧蚀性能较好,同时工艺性能优异;若耐烧蚀填料的用量过低且低于上述范围的最小值,则对耐烧蚀性能的提高不明显,无法发挥其本身的作用;相反地,若耐烧蚀填料的用量过高且高于上述范围的最大值,则混炼工艺困难,胶料粘性较大,同时出片困难,而且耐烧蚀填料的用量过高对烧蚀性能的提供也不明显。
进一步地,耐烧蚀填料的粒径对绝热层的力学性能对存绝热层的力学性能和耐烧蚀性能在较大的影响,经过大量试验证明,粒径为1~100μm时,绝热层的耐烧蚀性能和力学性能均较优,综合性能较好;若粒径过小且小于上述范围的最小值,填料很容易被烧蚀气流带走,无法达到固碳效果,对烧蚀性能的提供不显著;若粒径过大且大于上述范围的最大值,则填料在绝热层中的分散很难均匀,容易引起绝热层力学性能不同程度的降低。
在本发明一种优选的实施方式中,所述增塑剂为液体石蜡(lpo)、氯化石蜡、环烷烃油或高芳烃油中的一种或多种,优选为液体石蜡。
在本发明一种优选的实施方式中,所述金属氧化物为氧化锌或氧化镁中的一种其组合,优选为氧化锌。
在本发明一种优选的实施方式中,所述硫化剂为过氧化二异丙苯(dcp)、2,5-二甲基-2,5-二(过氧化苯甲酯)己烷、2,5-二甲基-2,5-双(叔丁基过氧基)己烷、2,5-二甲基-2,5-双(叔丁基过氧基)-3-己炔、过氧化二叔丁基(dtbp)、1,4-双(叔丁基过氧异丙基)苯、1,1-双(叔丁基过氧基)环己烷(dbpc)、或1,1-二(叔丁基过氧基)-3,3,5-三甲基环己烷(tmch)及其他有机过氧化物硫化剂。
在本发明一种优选的实施方式中,所述防老剂选自rd、mb、a、d、4010na、4010或aw中的一种多种。
在本发明一种优选的实施方式中,所述增粘剂为具有酚羟基的物质或多胺类物质,包括苯酚、邻甲苯酚、间甲苯酚、对甲苯酚、邻苯二酚、间苯二酚、萘酚或六亚甲基四胺中的一种或多种,优选为间苯二酚。
本发明中,采用特定的增粘剂作为改善绝热层纤维与橡胶基体结合力的改性剂,对与多种纤维填充epdm绝热材料具有较好的力学改善效果,特别是纤维填充后材料各向异性问题有较为明显的改善效果;经过研究发现,增粘剂的加入能够显著改善纤维、白炭黑等填料与基体间的作用力,显著提高材料内部的结构完整性,从而提高绝热层的力学性能,同时对改善混炼工艺具有较好的效果;若增粘剂的用量过高且高于上述范围的最大值,则会影响扰绝热层的混炼工艺,同时影响界面粘接性能;若增粘剂的用量过低且低于上述范围的最小值,则对绝热层力学,特别是平行方向的伸长率的提高不显著,无法和垂直方向的伸长率相比,从而使得两个方向的伸长率差异较大。
根据本发明的第二方面,提供了一种高能推进剂用耐烧蚀且力学性能优异的绝热材料的制备方法,用于制备上述第一方面所述的一种高能推进剂用耐烧蚀且力学性能优异的绝热材料,包括以下步骤:
步骤1,在10℃~50℃工况下,向密炼机中按比例依次加入三元乙丙橡胶、补强剂、有机纤维、增粘树脂、阻燃剂、耐烧蚀填料、增塑剂、金属氧化物、硬脂酸、防老剂密炼至均匀混合;
步骤2,在双辊开炼机上,向步骤1的物料中按比例加入硫化剂和增粘剂进行混炼,然后薄通6-10次后,最后薄通均匀出片;
步骤3,将步骤2中获得产物,通过在平板硫化机130~160℃下硫化40~400min成型,优选160℃下硫化40min成型,每降低10℃硫化成型时间增加一倍。
对本发明不做限制的,本发明人认为高能推进剂用耐烧蚀且力学性能优异的绝热材料及其制备方法的机理在于,采用多种耐烧蚀填料与大量有机纤维并用能够有效提高绝热材料的烧蚀性能,但有机纤维加入过多会严重影响绝热材料力学性能的发挥,通过在epdm绝热材料添加适量的增粘剂,能够在硫化过程中在硫化温度下反应生成具有继续反应能力的粘合树脂,而这种树脂几乎同时再进行与有机纤维的以化学键合和分子间作用为特征的粘合反应,以及与橡胶的以亚甲基桥和氧杂萘结构为特征的硫化反应。补强剂白炭黑的粒子表面具有酸性硅烷醇结构,对间-甲粘合树脂的生成起催化作用,能够显著改善有机纤维与橡胶基体的结合力,从而显著改善绝热层的力学性能,适用于高能推进剂对耐烧蚀绝热层力学性能的要求,并得到一种性能优良的绝热材料,同时能够满足发动机内绝热材料对粘接性能,以及耐烧蚀与抗冲刷性能等综合性能的要求。
实施例
在以下各种实施例中,线烧蚀和质量烧蚀率均按国军标《gjb323b-2018烧蚀材料烧蚀试验方法》的规定测定,测试条件为:喷嘴直径为2mm,烧蚀距离10mm,氧气气压0.4mpa,乙炔气压0.1mpa,氧气流量0.6m3/h,乙炔流量0.68m3/h,,烧蚀时间20秒;拉伸强度和断裂伸长率均按《q/g197-2008固体火箭发动机燃烧室绝热层、衬层材料抗拉强度、断裂伸长率测定方法》标准中规定测试隔热材料在20℃,100mm/min的拉速下的力学性能;粘接性能按《gb11211-1989硫化橡胶与金属粘合强度的测定拉伸法》标准中规定测试隔热材料在20℃,20mm/min的拉速下的粘接强度。
实施例1~5
实施例1-5所用隔热材料原料组成见表1
表1实施例1~5绝热材料的原料组成
(1)备料:按照表1中实施例1-5的原料组分备料。
(2)混炼:按照epdm薄通3遍→有机纤维pa+pi→耐高温树脂颗粒pps→zno、tx→sio2→lpo→app→rd→ys→dcp硫化剂→增粘剂zn(间苯二酚)→薄通6遍→薄通出片的顺序炼制epdm绝热材料。
制备混炼胶时,要注意混炼温度(为110℃),避免在温度过高时将硫化剂和增粘剂剂加入,以免使胶料发生焦烧,影响材料的性能及使用。混炼操作正确的作法是密炼结束后将胶料放置一段时间,等胶料冷却后,之后再将硫化剂和增粘剂加进去。混炼好的胶料在使用前应密封避光储存。
(3)制样:制备2mm厚的胶片,用于测试力学性能、密度、热导率及玻璃化温度;制备φ30mm×10mm的烧蚀件5个;用于测试烧蚀性能,制备φ40mm×3mm的粘接件5个,用于测试粘接性能;硫化条件为:160℃×40min×5mpa。
(4)性能测试:按照相应的标准和规范测试绝热材料的各项性能,具体结果见表3。
对比例1~3
对比例1-3所用绝热材料的原料组成见表2
表2对比例1~3绝热材料的原料组成
(1)备料:按照表2中对比例的原料组分备料。
(2)混炼:按照epdm薄通3遍→有机纤维pa→zno、tx→sio2→lpo→app→rd→ys→dcp硫化剂→薄通6遍→薄通出片的顺序炼制epdm绝热材料。
制备混炼胶时,要注意混炼温度,避免在温度过高时将硫化剂加入,以免使胶料发生焦烧,影响材料的性能及使用。混炼操作正确的作法是密炼结束后将胶料放置一段时间,等胶料冷却后,之后再将硫化剂和增粘剂加进去。混炼好的胶料在使用前应密封避光储存。
(3)制样:制备2mm厚的胶片,用于测试力学性能、密度、热导率及玻璃化温度;制备φ30mm×10mm的烧蚀件5个,用于测试烧蚀性能;制备φ40mm×3mm的粘接件5个,用于测试粘接性能;硫化条件为:160℃×40min×5mpa。
(4)性能测试:按照相应的标准和规范测试绝热材料的各项性能,具体结果见表3。
表3实施例和对比例的绝热材料性能对比
绝层材料的指标要求及实施例、对比例性能指标如下表4:
表4绝层材料的指标要求及实施例、对比例性能指标
由表3和表4数据可以看出,对比例绝热材料垂直方向力学性能较好,密度较低,界面粘接性能也较好,但平行压延方向,绝热层材料的力学性能较差,无法满足发动机特殊条件下对力学性能的要求,同时因为只有一种纤维,导致材料耐烧蚀性能较差,同时通过性能优化,无法满足发动机对烧蚀性能和抗冲刷性能的更高要求,无法满足指标要求;而采用耐烧蚀填料与大量多种纤维,并适量加入增粘剂改善绝热层的力学性能,不仅垂直方向力学性能较好,耐冲刷和耐烧蚀性能更加优异,而且在平行方向的力学性能也非常优异,能够充分满足发动机对绝热层力学性能的特殊要求,同时密度与之前相当,在同等厚度条件下不会显著增加绝热层的质量;而且由于耐蚀性性能更优,可以降低绝热层厚度,显著降低绝热层的质量,从而降低发动机的消极质量,最终提高发动机的射程。同时对比例和实施例,绝热层的热导率和玻璃化温度基本相当,增加增粘剂后界面的粘接性能略有提高,能够提高绝热层使用的可靠性,保证界面粘接性能可靠。
采用弯管烧蚀发动机来模拟发动机的烧蚀考核试验,以考核实施例1和对比例2绝热材料的抗粒子冲刷能力,推进剂选用改性三组元,发动机喷管喉径为13mm,工作压强约为2.1mpa,工作时间约为8.0s。实施例1和对比例2绝热材料的弯管烧蚀情况如表5和图1~2所示。
表5弯管烧蚀结果及对比
由表5和图1可知:实施例1绝热层烧蚀最严重区域约在70mm处,约烧掉13.2mm厚,对比例2绝热层烧蚀最严重部位约在75mm处,约烧掉14.94mm厚,约比实施例1多烧掉10%,可见对比例2绝热材料的抗粒子冲刷能力没有实施例1优异。图2a为实施例1烧蚀结果图,图2b为对比例2烧蚀结果图。
以上结合具体实施方式和范例性实例对本发明进行了详细说明,不过这些说明并不能理解为对本发明的限制。本领域技术人员理解,在不偏离本发明精神和范围的情况下,可以对本发明技术方案及其实施方式进行多种等价替换、修饰或改进,这些均落入本发明的范围内。本发明的保护范围以所附权利要求为准。
本发明说明书中未作详细描述的内容属本领域技术人员的公知技术。
起点商标作为专业知识产权交易平台,可以帮助大家解决很多问题,如果大家想要了解更多知产交易信息请点击 【在线咨询】或添加微信 【19522093243】与客服一对一沟通,为大家解决相关问题。
此文章来源于网络,如有侵权,请联系删除


